Materials Science
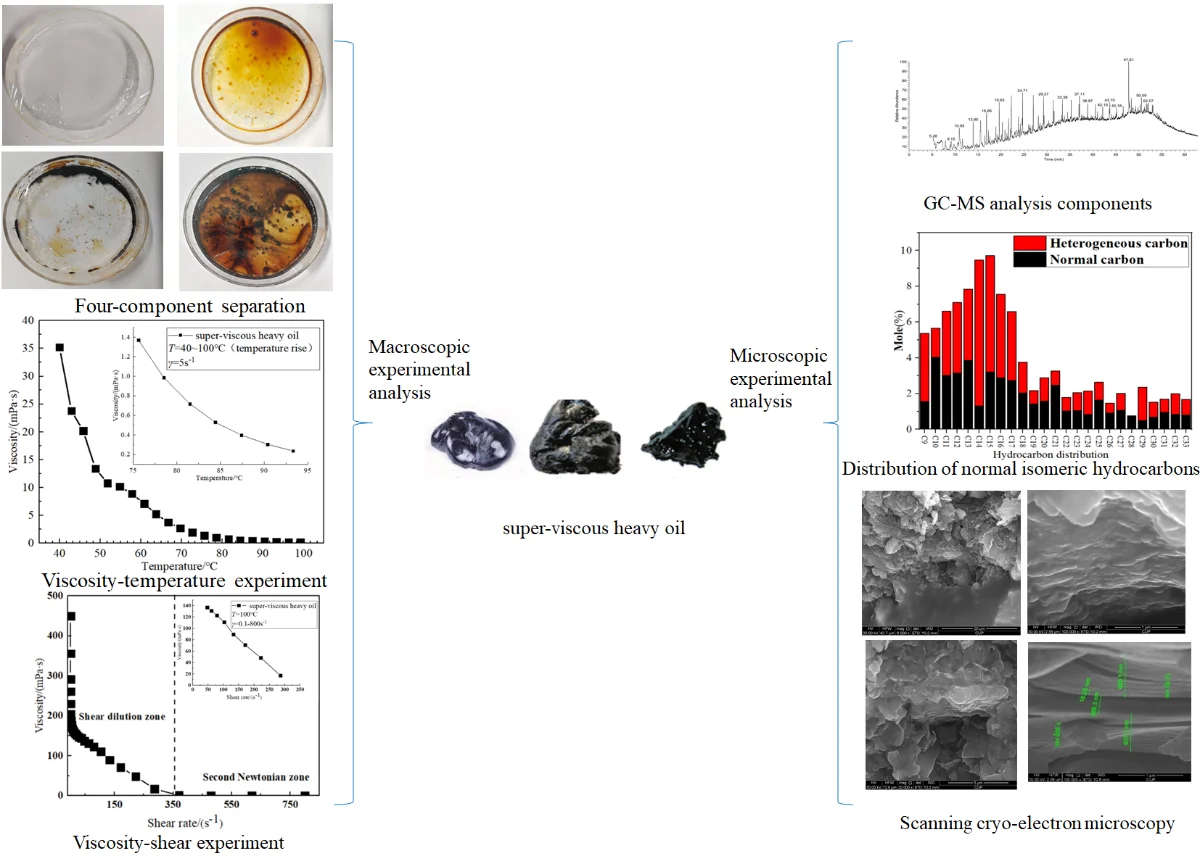
Editor's pick
Research Article
Experimental study on the rheological characteristics and viscosity-enhanced factors of super-viscous heavy oil
By Yang Chen, Jin Luo, Meiyu Zhang, Minglan He
To reveal the viscosity-enhanced mechanism of super-viscous heavy oil and improve the recovery rate of super-viscous heavy oil, the four components, elemental composition, rheological properties, and effects of asphaltenes and resin on the viscosity of super-viscous heavy oil from well TH12434 in Tahe Oilfield, China have been analyzed from macro and microscopic perspectives by Anton Paar rotational rheometer, gas chromatography-mass spectrometry and scanning cryo-EM to solve the problems of poor fluidity and high asphaltene content. The experimental results showed that in the temperature range of T= 40-100°C, the viscosity of super-viscous heavy oil decreases sharply from 352000 mPa∙s to 1620 mPa∙s, and the super-viscous heavy oil exhibits clear thermo-sensitivity. With T= 100°C and shear rate ranging from γ= 0-800 s-1, the viscosity of super-viscous heavy oil decreases sharply from 45000 mPa∙s to 956 mPa∙s, and the oil sample shows typical pseudoplasticity. The baseline of super-viscous heavy oil analysis by gas chromatography shows too high, and more than 80 % of super-viscous heavy oil compounds have a matching degree of less than 70 % with standard compounds, indicating that the super-viscous heavy oil had poor heterogeneity and many impurities. It is observed by scanning cryo-EM that the micromorphology of super-viscous heavy oil is large granular, strong continuity, asphaltene micromorphology presents an obvious layered structure, the layer spacing is 637.7 nm, and its asphaltene molecules form an order-like or crystal-like association structure through several unit sheet layers, resulting in high viscosity of super-viscous heavy oil. Based on the analysis results of the influencing factors of the viscosity of super-viscous heavy oil, a theoretical basis for the selection of viscosity reduction technology for super-viscous heavy oil the efficient exploitation in Tahe Oilfield, China could be provided.
November 7, 2023
Industrial Engineering
Most cited
Research Article
A conversion guide: solar irradiance and lux illuminance
By Peter R. Michael, Danvers E. Johnston, Wilfrido Moreno
December 4, 2020
Applied Physics
Most cited
Research Article
Experimental kinematic analysis of an intermittent motion planetary mechanism with elliptical gears
By Alexander Prikhodko
September 30, 2020
Applied Physics
Most cited
Research Article
Experimental analysis of cutting force during machining difficult to cut materials under dry, mineral oil, and TiO2 nano-lubricant
By I. P. Okokpujie, L. K. Tartibu
December 13, 2021
Applied Physics
Most cited
Research Article
Experimental and finite element approach for finding sound absorption coefficient of bio-based foam
By L. Yuvaraj, S. Jeyanthi, Lenin Babu Mailan Chinnapandi
September 30, 2019
Public Health
Liquid and Gaseous Energy Resources
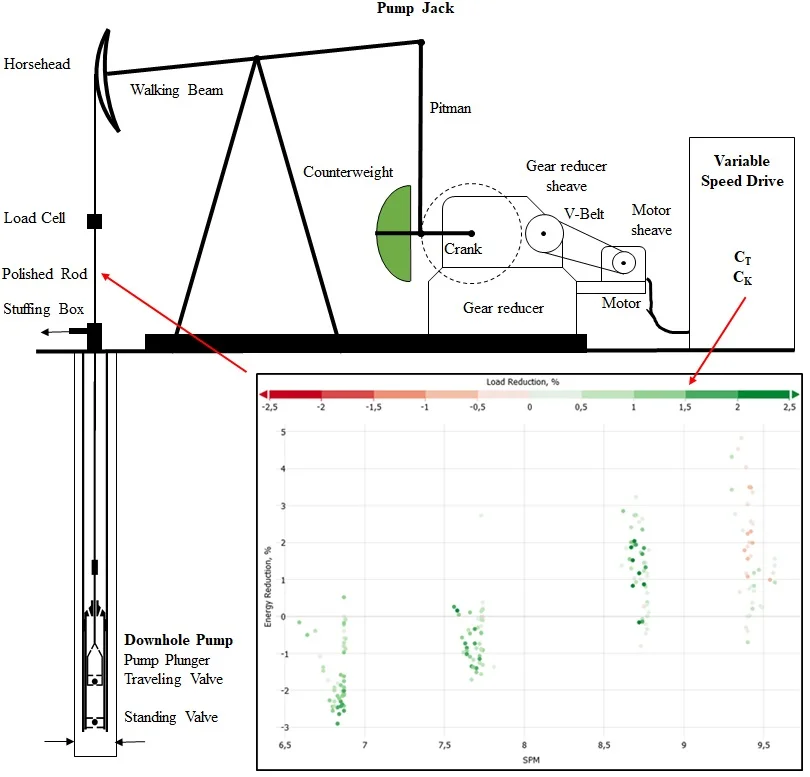
Research Article
Sucker rod pump frequency-elastic drive mode development – from the numerical model to the field test
A frequency-elastic drive mode for a sucker rod pumping system is introduced to reduce its polished rod peak loads and the total energy consumption. Numerical modeling and an extensive field test verify the concept. The frequency-elastic drive mode is a software solution for variable speed drive systems, which can be applied in the controller and does not require any hardware adjustments. The novel drive mode adjusts the set frequency, sent by the controller to the frequency converter, depending on the actual power requirements. An increase in power consumption results in a reduction of the set frequency, which is proportional to the power consumption increase. A reduction in power consumption results in the opposite effect to achieve a similar pumping speed as for regular operation. The frequency-elastic drive mode is simulated by a numerical model, which covers the entire pumping system. An extensive field test was performed to verify the concept and the numerical model. The simulation and the field test have confirmed the concept of the frequency-elastic drive mode and quantified its saving potential. The evaluation of the field test has shown that the energy-saving potential can reach five percent. In addition, a peak polished rod load reduction of up to three percent was seen. At the tested pumping system the frequency elastic drive mode under optimized parameters yields the best results in terms of total energy savings in the pumping speed range between 7 to 10 strokes per minute. A downhole system efficiency increase was seen for any pumping speed. The numerical model matches the field test data and allows the performance prediction of the novel drive mode for changed parameters and wellbore configurations without extensive field testing. The novelty of the presented paper is the concept of the frequency-elastic drive mode, which is a pure software solution for variable speed drive sucker rod pumping systems. The holistic model includes the entire pumping system and matches the field test data at remarkable accuracy.
June 21, 2021
Industrial Engineering
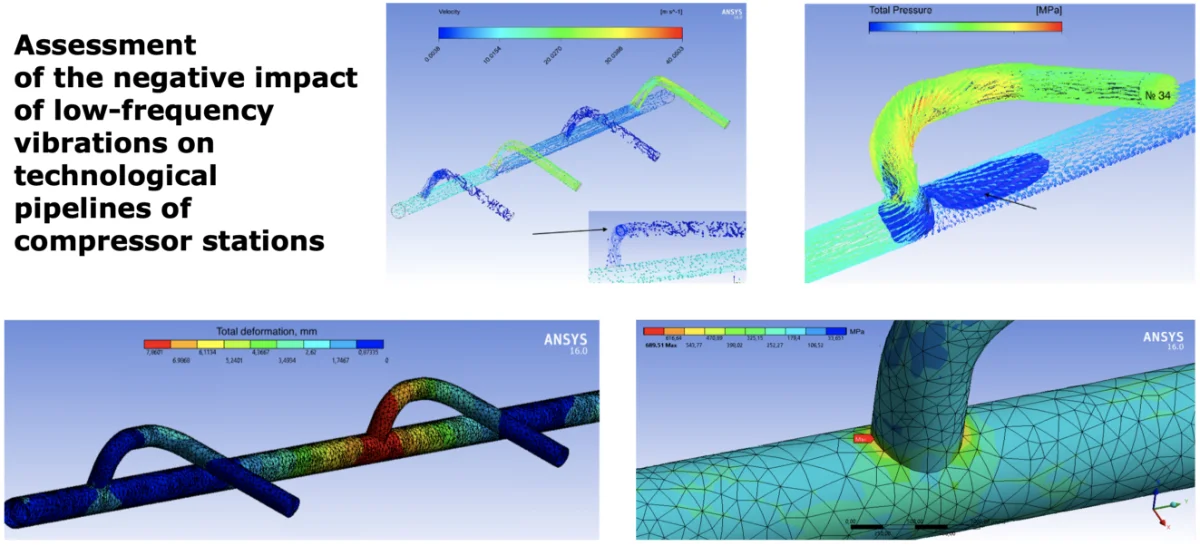
Research Article
Assessment of the negative impact of low-frequency vibrations on technological pipelines of compressor stations
The intensive development of gas transport and compressor manufacturing aimed at increasing the unit capacities of gas pumping units, creating high-flow centrifugal compressors, increasing the productivity of compressor shops has led to the appearance of fundamentally new problems in the diagnosis of industrial pipelines. The reasons for premature failure of piping manifold of gas pumping stations can be associated with both high static voltage in the pipelines and a high level of vibration. The main reasons for the increased vibration of the technological pipelines of the centrifugal compressor can be significant disturbing forces of the gas flow, coincidence of the natural frequencies of the pipeline system elements with frequencies of the disturbing forces, low dynamic stiffness of the pipeline- support system or a combination of the above conditions. The most effective method for studying problems such as low-frequency vibrations is the combination of engineering means for calculating dynamic processes and the results of measurements of the parameters of these processes in real systems and operating modes of the compressor stations. The hypotheses of the occurrence of low-frequency vibrations in pipelines are considered during the study, the acoustic properties of the process piping, and the resonant vibrations conditions are calculated. A computer model was created in the ANSYS Workbench software in order to consider the loading conditions for process piping. Based on Gazprom company standard 2-2.3-324-2009, an algorithm is proposed that is of practical importance for engineers of plant diagnostics operating gas transmission equipment. It is proposed to combine the performance of vibroacoustic studies and computing modeling with the determination of trends in the technical condition of the system for the analysis of changes in vibro-parameters. As a result of the work, direct measurements of the vibrodiagnostic specialists of the operating compressor station were compared with the obtained modeling data. Some methods were proposed to reduce the impact of operating conditions and design of the process piping on unacceptable low-frequency vibrations.
June 25, 2021
Industrial Engineering
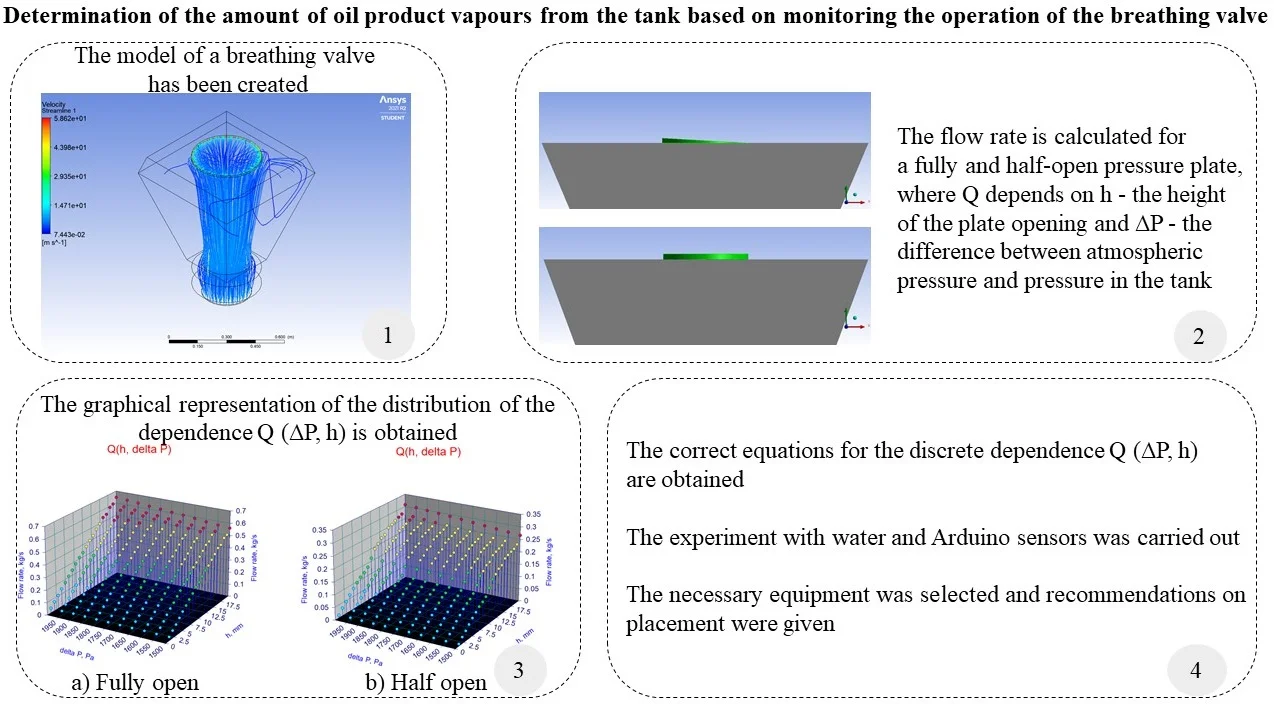
Research Article
Determination of the amount of oil product vapours from the tank based on monitoring the operation of the breathing valve
The development of methods for calculating losses of oil and petroleum products vapours from the tank has been going on for a long time. Systems that allow for more accurate calculations are also being developed along the way. In each country, and sometimes in each company, there are their own methods for determining the loss of light hydrocarbon fractions from losses from the tank through the breathing valve. In addition, losses are divided into “working losses” and “standing losses”. In each technique, there are both pros and cons. The most characteristic disadvantage of each technique is its applicability only to the conditions in which it was developed, due to the presence of correction coefficients. This article proposes a new technique for determining the loss of hydrocarbons vapours from the tank through the breathing valve, both from “working losses” and from “standing losses”. In the course of the work, formulas were obtained for calculating the flow rate Q∆P,h through the breathing valve, which depends on the degree of opening of the pressure plate and overpressure. An experiment was conducted, instrumentally proving the application of the developed methodology. And also, the equipment is selected and recommendations on its installation and use are given.
June 30, 2022
Industrial Engineering
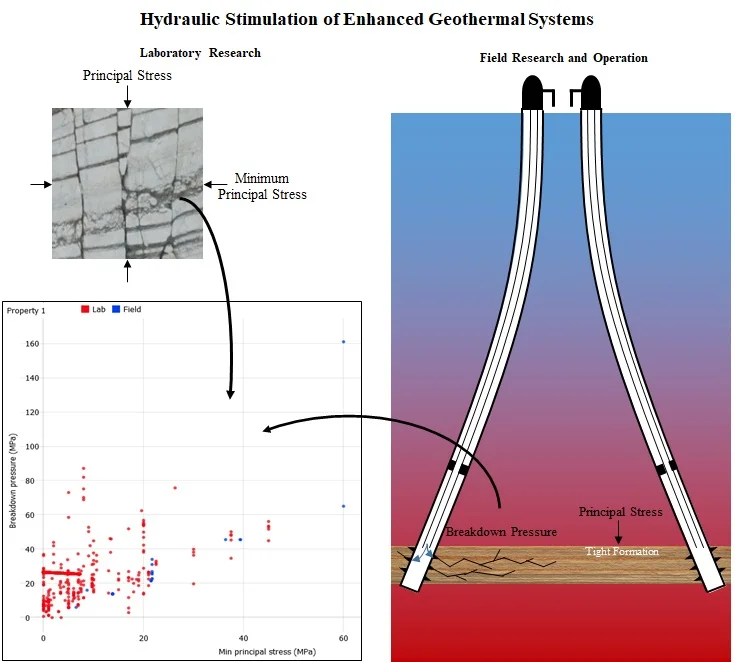
Research Article
A holistic review on hydraulic fracturing stimulation laboratory experiments and their transition to enhanced geothermal system field research and operations
This paper presents a thorough overview of hydraulic stimulation techniques, conducted in laboratories. It further analyses field experiments and ongoing projects for geothermal energy production to investigate if the findings from the lab can be practically applied to the field. Stimulation techniques have been long used in the oil and gas industry as a means to increasing the rock permeability and consequently the reservoir’s fluid production rate. Among the different stimulation methods, hydraulic fracturing is known to be the most successful in creating new passageways in the formation. Nevertheless, the benefits of fracturing have been hindered by the handful of events in which poor planning had led to severe seismic activities. Therefore, across the globe, many efforts were dedicated to characterizing fracture creation and propagation in different rocks, not only to provide know-how for further and safer developments in the oil and gas front but also to adapt such findings to the ever-emerging field of geothermal energy recovery. In the course of this work, over 100 papers were studied. The papers included laboratory experiments on various rock types encountered in reservoirs, where parameters such as stress regime, fracture initiation pressure, formation breakdown pressure, volume, and types of fluid injected were monitored. To investigate whether or not such practices had been previously applied in geothermal energy production, a thorough study was also conducted on large-scale experimental setups constructed in the field as well as hydraulic fracturing procedures performed in operational projects, going back as far as a decade. The results show an agreement between laboratory experiments and field operations, yet naturally including individual results from cases where either the lab parameters or field characteristics were extraordinarily unique. Multiple cross-correlations were also performed between different key parameters that play a role in a fracturing process, providing trends that could be intra- or extrapolated for further research and planning. The novelty of this work is the comprehensive analysis of numerous research projects done around the world. As a result, this paper will not only be an informative and yet compacted source of information concerning previous projects, but it also points out the main factors and their relationships which need to be understood to guide a future project to success.
June 21, 2021
Industrial Engineering
Liquid and Gaseous Energy Resources
Devoted to transportation of liquid and gaseous energy resources: hydrocarbons, crude oil, oils, petroleum, water, hydrogen, biofuel
APC
Free of charge
Best of Theme
Most cited
Research article
January 22, 2021
Design of low-cost wireless noise monitoring sensor unit based on IoT concept
By Maja Anachkova, Simona Domazetovska, Zlatko Petreski, Viktor Gavriloski
Most cited
Research article
June 29, 2020
Nondestructive microparticle analysis method
By Vadim Rybin, Semyon Rudyi, Olga Kokorina
Most cited
Research article
June 30, 2022
The vibration of a thermoelastic nanobeam due to thermo-electrical effect of graphene nano-strip under Green-Naghdi type-II model
By Hamdy M. Youssef, Abdullah A. Al Thobaiti
Most cited
Research article
May 15, 2019
Joint parameter identification, vibration and noise analysis of gearbox
By Tengjiao Lin, Daokun Xie, Quancheng Peng, Songling Guo, Hesheng Lv
You might also like
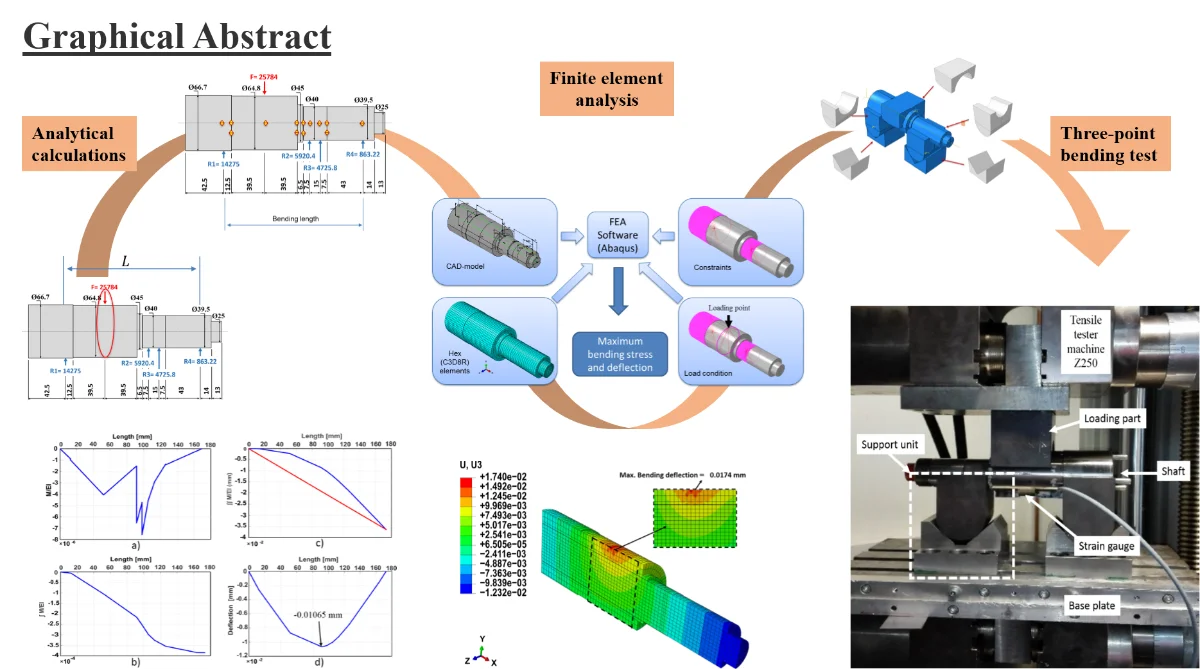
Most downloaded
Research Article
FE analysis and experimental determination of a shaft deflection under three-point loading
By Bernd Engel, Sara Salman Hassan Al-maeeni
Increasing industrial demand for new products including advanced production technology leads to substantial natural resources consumption. Furthermore, huge environmental pollution and emerging environmental legislation motivate the machine tools industry as one of the major resource consumers on a global scale to develop methods for more sustainable use of the Earth's resources. Machine tools re-engineering concerning design and failure analysis is an approach by which outdated machines are upgraded and restored to like-new machines. To evaluate the mechanical failure of the used machine components and to ensure their reliable future performance, it is essential to make material, design, and surface investigations. In this paper, an experimental approach based on the principle of a three-point bending test is presented to evaluate the shaft elastic behavior under loading. Moreover, finite element analysis and numerical integration method are used to determine the maximum linear deflection and bending stress of the shaft. Subsequently, a comparison between the results is made. In conclusion, it was found that the measured bending deflection and stress were well close to the admissible design values. Therefore, the shaft can be used again in the second life cycle. However, based on previous surface tests conducted, the shaft surface needs re-carburizing and refining treatments to ensure the reliable performance of the surface.
September 24, 2018
Applied Physics
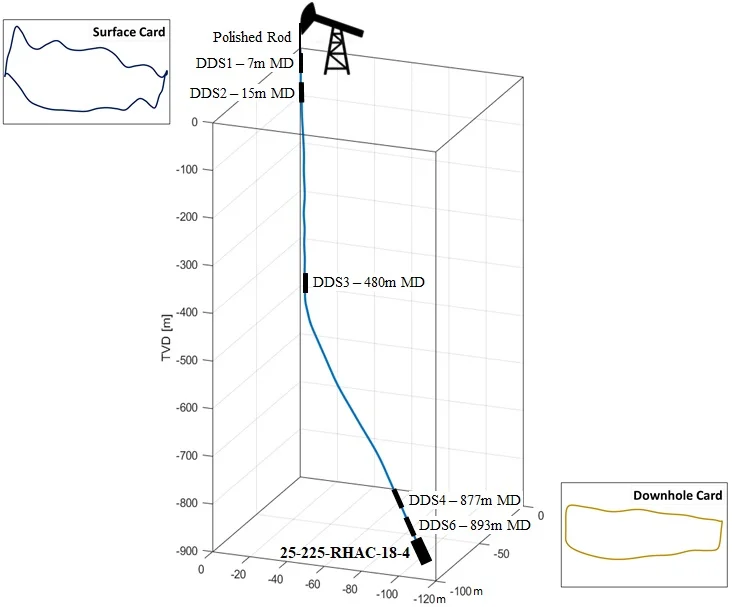
Most downloaded
Research Article
Sucker rod pump downhole dynamometer card determination based on a novel finite element method
By Patrick Eisner, Clemens Langbauer, Rudolf Fruhwirth
An advanced dynamic finite element model is presented that diagnoses the downhole pump performance of sucker rod pumping systems, applicable for any pumping conditions and equipment used. The results are compared to downhole measurements and other evaluation techniques. Buckling is an undesirable phenomenon occurring in sucker rod pumping. It essentially depends on the plunger load, which is a function of time and typically not measured but evaluated by diagnostic tools. Existing diagnostic tools exhibit specific limitations that reduce their applicability and output quality. This paper introduces a diagnostic tool, which can predict the rod string's stress field and its movement not only at the pump plunger but all along the rod string. Moreover, this tool can account for the interaction between rod guides and tubing as well as rod string and tubing. To this end, innovative tube-to-tube contact modeling is applied. The high precision results are accomplished by running a dynamic finite element simulation. The basic principle is to evaluate the plunger load incrementally by consecutively applying restarts of each time step, fully automated and computation time optimized. This publication shows that both the plunger load and the rod string’s dynamic behavior can be determined for any given wellbore as long as the borehole trajectory and surface dynamometer measurements are known. The dynamic finite element model is evaluated for a deviated system and a vertical system equipped with two different downhole pump types. Comparing the simulation results with the available downhole measurements and the analytical solution shows an excellent match, whereas the proposed solution provides a considerable amount of details about the overall system’s behavior. The evaluation has shown that the performance of standard and novel downhole pump types can be successfully diagnosed in detail, which is just possible under limitations with commercial software solutions. This tool can correctly predict whether or not the sucker rod string is subjected to buckling during the downstroke, which has a considerable effect on increasing the mean time between failures of a sucker rod pumping system. From the economic point of view, this means that the economic limit of a wellbore can be postponed. The novelty of the shown technique is the consideration of the full 3D trajectory and the implementation of only physical properties, result in an excellent accuracy of the output.
June 21, 2021
Industrial Engineering
Error correction and uncertainty measurement of short-open-load calibration standards on a new concept of software defined instrumentation for microwave network analysis
Software-Defined Radio (SDR) has appeared as a sufficient framework for the development and testing of the measurement systems such as a signal generator, signal analyzer, and network analysis used in the network analyzer. However, most of researchers or scientists still rely on commercial analyzers were larger benchtop instruments, highly cost investment and minimum software intervention. In this paper, a new concepts measurement revolution called as Software Defined Instrumentation (SDI) on network analysis is presented, which is based on reconfigurable SDR, a low-cost implementation, ability to access RF chain and utilizing open source signal processing framework. As a result, a Vector Network Analyzer (VNA) has been successful implemented by deploying an SDR platform, test sets, and data acquisition from the GNU Radio software in host PC. The known calibration process on SHORT-OPEN-LOAD (SOL) technique is validated to ensure measurement data from this SDI free from systematic error. Two types of SOL calibration standards used for a comparison study to validate the SDI measurement system which is capable of generating the response on the differential of standard quality and accuracy of standards kits. Finally, calibration uncertainty analysis is also presented in this work by utilizing RF open source package without any cost addition.
Effect of heat transfer optimization on brake noise characteristics of automotive disc brake
Heat effect is one of the most important factors affecting the brake noise level. The finite element model for transient heat transfer analysis of disc brake is established based on heat transfer control equation and heat dissipation boundary conditions of dynamic convection. According to the NVH test and modal calculation, the brake noise characteristics are tested and analyzed. Meanwhile, the heat transfer simulation is verified and shows high accuracy. The discrete data for the response surface function are obtained by the Central Composite Design method with the peak temperature and mass as the target variables. The error of regression function is judged by fitting decision coefficient, correcting decision coefficient and root mean square error. By the optimizing mathematical model, the brake disc temperature peak can be greatly reduced and the heat transfer ability is obviously optimized without mass increasing, the time with temperature above 120 °C can be reduced by 46 %. Through the comparison of brake noise level before and after optimization, it can be known that the noise level can be significantly decreased after structural optimization, except the first order resonance frequency. The optimization result has good social and economic value.