Abstract
Common Portland cement was used as the main matrix material and cementations material, fly ash as admixture, 30 % wt hydrogen peroxide as foaming agent and other additives to prepare cement based condensate porous material. The optimum amount of foaming agent was determined by water absorption and release experiment, and the metal fiber was added to the material to enhance the water collecting performance. As the amount of foaming agent increased, water absorption increased, water release rate decreased, the optimum content of foaming agent was 2.73 %, the material had better water absorption and water release performance, and the addition of metal fiber could obviously improve the water collection performance of cement-based porous condensate material.
1. Introduction
Land desertification refers to the drought, semi-arid and dry semi-humid areas, due to climate change and human activities, a kind of land degradation phenomenon [1], is one of the most serious ecological environmental problems in the world, its formation and expansion not only seriously damage the ecological environment, but also cause immeasurable damage to social civilization, economic development, has received widespread attention around the world [2]. According to the results of the fifth Chinese desertification and desertification monitoring, the national desertification land area is 1.72 million km2 [3], Therefore, as a country extremely seriously affected by desertification hazards, desertification control work is urgent, and the insufficient water supply caused by less precipitation and large evaporation is the key [4] restricting the vegetation recovery in desertification areas. The source of water in the desert is divided into artificial foreign water, groundwater, sand adsorption water, precipitation and air water [5], including precipitation and air water content, and artificial foreign water and groundwater consume huge manpower and material resources, high cost of [6], and easy to cause huge water waste [7], in recent years has gradually [8] criticized by scholars from all walks of life. Therefore, how to use sand grains to absorb water to achieve the purpose of vegetation restoration is an important topic in the problem of desert ecological restoration. Finding a low-cost watering-free technology will become a new means of desertification control, and foam concrete is an investigable direction.
Foam concrete is a building material with strong biocompatibility [9]. By mixing cement, admixtures, additives and other materials, mixing, molding and mold curing. Its interior contains a large number of uniform and small pores [10-14], so it is also known as foaming cement. It is a new type of waste benefit, environmental protection, energy saving material [15], but the current application is relatively limited, mostly used in housing insulation and heat insulation [16], sound insulation [17], fire retardant [18], shock prevention and shock absorption [19], pollution absorption [20] and other fields, in the field of desertification control, is basically still in the laboratory stage. Different from thermal insulation, sound insulation and other fields of foaming cement materials need very low water absorption rate [21] (generally require water absorption rate in more than ten percent or even several percent), applied to desertification treatment of foam cement materials require higher water absorption rate [22], generally required in more than 30 %, so that it may be widely used in desertification areas with very little precipitation and sediment water content. Therefore, the key to this technology is how to improve the water absorption and water collection performance of foaming cement.
In response of this question, The preparation process of foaming cement is taken as the main method, Ordinary silicate cement, deionized water as the main raw materials, Doped with small amounts of fly ash and other additives, Hydrogen peroxide is also used as a foaming agent, Cement-based porous condensation material was prepared by alkali excitation reaction at low temperature (35-50 ℃), The effects of the content of foaming agent on pore structure, average pore diameter and absorbance and release were studied, On this basis, metal fiber adds the inner hole of the cement-based porous condensation material, To explore its influence on the collecting properties of the material, To lay the foundation for its application in the field of desertification control.
2. Materials and methods
2.1. Materials
Common silicate cement (P·O52.5, The density was 3.123 g/cm3, Shandong Zhucheng Yangchun Cement Co., Ltd.); Fly ash (FA, For the next 500 entries, Zhengzhou First Power Plant), silicone polyether (MPS, Purity of > 96 %, Linyi Lvsen Chemical Co., Ltd.), lithium carbonate (Li2CO3, Purity of > 98 %, Shanghai Industrial Co., Ltd), hydrogen peroxide (H2O2, 30 % wt, Beijing Chemical Plant); Deionized water (H2O, Laboratory b homemade), Metal fibers (MF, 316 Stainless Steel, Guangzhou Weishi Hardware Stainless Steel Products Factory).
2.2. Determination of the foaming agent content
88 g of ordinary silicate cement, 10 g of fly ash, 2 g of silicone polyether, and 0.04 g of Li2CO3 were taken by the PL203 electronic balance, the silicone polyether is an anionic surfactant that plays a bubble-stabilizing role throughout the reaction, and Li2CO3 plays an accelerated hardening role of the slurry. After the above dry powder material is mixed, stirred evenly, adding 46 g of deionized water according to the water ash ratio of 0.46. Mechanical stirring 3 min, with DJ1C-200 electric mixer at room temperature to form cement slurry. Based on the dry powder material, inject 2 %, 2.5 %, 3 %, 3 %, 3.5 % and 4 % for another 30s.The stirred slurry was then poured evenly into a 50 mm diameter mold, placed in a QHP-70BE artificial climate box, control relative humidity of 70 %, temperature of 40 ℃, 12 h removal, and 7 d, at room temperature to obtain the required foam cement test.
2.3. Preparation of cement-based porous condensation material
Different proportions of metal fiber (Metal Fiber) were added to the experiment (1) with 0.09 mm, 0.10 mm, 0.15 mm, diameter of 0.2 %, 0.4 %, 0.6 %, 0.8 %, 1.0 % (dry powder material base). The second batch of cement-based porous condensation material was prepared completely according to the experimental process of the experiment (1), and a blank control group without addition of metal fiber was set. The metal fiber acts as a cold body inside the bubble hole of the material, and has the effect of rapid condensation of water vapor.
2.4. Performance test and characterization of cement-based porous condensation material
Water absorption rate test: the polished round cake sample is dried in the drying box with the electronic balance until the quality is no longer changed, recorded as , and then soak in water for 48 h at room temperature until no longer absorb water. After removing the sample, absorb the water attached to the sample surface with dry tissue, and then immediately measure the quality , to calculate the water absorption rate of the material according to the Eq. (1):
Water release rate test: put the sample of mass on the test table and evaporate the water on the surface and interior naturally at room temperature, measure the quality , of the , of the material is finally calculated according to the Eq. (2):
where is the release time, unit h, is the total water weight and unit g.
Water collecting performance test: Build the water collecting experimental platform as shown in Fig. 1, and the sample is fixed on the experimental platform. After a period of time, the change in sample quality , and the water collection efficiency of the material is finally calculated according to the Eq. (3):
where is the water collection time, unit h, is the sample collecting mist surface area and unit m2.
Fig. 1Water gathering system experimental platform
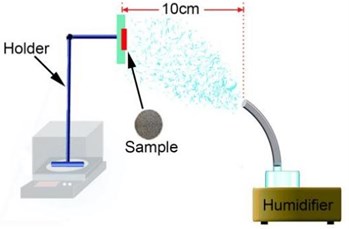
3. Results and discussion
3.1. Effect of foaming content on the absorbent ability and release properties of foaming cement
The effect of the content of hydrogen peroxide foaming on the absorbent energy and release properties of the foaming cement is as shown in Fig. 2. As can be seen from the figure, the higher the foaming agent, the higher the water absorption rate of the material and the lower the water release rate. This is because the higher the content of the foaming agent, the larger the bubble pore diameter of the cement-based porous condensation material, the more the through holes formed by the connection between the bubbles, the more water into the material, so the higher the water absorption rate. In the water release link, the water inside the material will also be released into the air through these through hole channels. The material with larger pore diameter passes through the holes, and the water release rate is faster, while the bubble hole with smaller aperture forms less through holes, and the water release rate is slower. The intersection of the water absorption curve and the water release rate curve in Fig. 2 is the water absorption energy and water release performance of the cement-based porous condensation material. The transverse coordinate of this point is 2.73, that is, the content of the foaming agent is 2.73 %, the corresponding material is 31.8 %, and the release rate is 3.36 h/g, material has good water absorption energy and water release performance.
Fig. 2Relationship between water absorption and water release time of foam cement
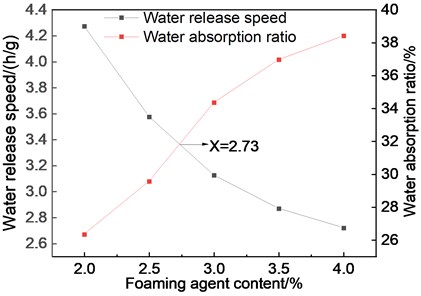
3.2. Effect of metal fiber on cement-based porous condensate material and collecting mechanism
The control foaming content was optimal, namely 2.73 %, and the effect of the diameter and content of the metal fiber was studied by preparing the cement based porous condensation material sample and the control group without metal fiber.
Fig. 3Effect of metal fiber addition on water collection of cement-based porous condensate materials
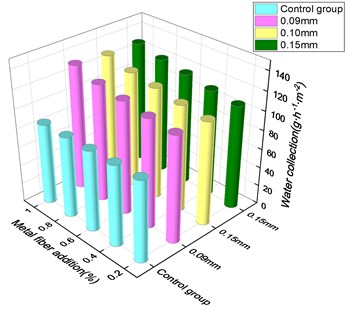
The effect of the diameter and content of the metal fibers on the collecting properties of the cement-based porous condensation material is shown in Fig. 3. It is seen from figure that the material catchment performance after adding metal fibers was generally better than the control group. And the diameter of metal fiber has less impact on the collecting properties of cement-based porous condensate material, The addition of metal fiber has a great impact on the catchment performance of the material, The effect of the diameter of metal fiber on the cement-based porous condensation material also affects the sample through the amount of factors: for metal fibers of the same quality and different diameter, the number is different, the greater the diameter difference, the more the number difference, that is, the larger the added amount gap, this is also confirmed by the fact that 0.09 mm and 0.10 mm closely approximate the height of 0.15 mm; Also, Metal fibers of the same mass percentage, The larger the diameter of the metal fibers, the larger the surface area is, the higher the water collection efficiency it is. The catchment performance of the material increases with the addition of metal fibers, where the material has the optimal catchment performance with a 0.09 mm, added diameter of 1 %, reaching 132.46 g·h-1·m-2, at 1.54 times that of the control group sample. This is because the specific thermal capacity of the metal fiber is much higher than the material matrix, while the thermal conductivity is lower, so the water vapor around it is more likely to cool to the dew point and condense into liquid water, the more metal fiber added, the stronger the condensation effect.
4. Conclusions
With the increasing content of hydrogen peroxide foaming, the water absorption rate of cement-based porous condensation material increases and the water release rate decreases. When the amount of foaming agent is 2.73 %, cement based porous condensation material has good water absorption energy and water release properties.
The addition of metal fiber can significantly enhance the collecting performance of cement-based porous condensation material, and the diameter of metal fiber has a small impact on the collecting performance of the aggregate content of the material is 0.2-1 %. In them, the diameter of 0.09 mm, is 1 %, reaching 132.46 g·h-1·m-2, by 54 % compared with the control group.
References
-
S. P. Yu, “Causes, Harm of terrain desertification and the policy of restoration,” (in Chinese), Environmental Science and Management, Vol. 31, pp. 16–17, 2006.
-
“United Nations Convention to Combat Desertification in Those Countries Experiencing Serious Drought and/or Desertification, Particularly in Africa,” China Forestry Publishing House, Beijing, Combat Desertification Office of Ministry of Forestry in the People’s. Republic of China, 1994.
-
Z. F. Tu, M. X. Li, and T. Sun, “The status and trend analysis of desertification and sandification,” Forest Resources Management, Vol. 1, pp. 1–5, 2016, https://doi.org/10.13466/j.cnki.lyzygl.2016.01.001
-
U. Tanaka et al., “Practical technique sand extension method for desertification control in the Sahel west Africa,” Journal of Disaster Research, Vol. 8, pp. 125–126, 2013.
-
Z. Zhang, H. Du, and Y. Qu, “Review on desert water science materials,” Materials China, Vol. 37, No. 2, pp. 81–87, Feb. 2018, https://doi.org/10.7502/j.issn.1674-3962.2018.02.01
-
J. Zhang et al., “Is the Taklimakan desert highway shelterbelt sustainable to long-term drip irrigation with high saline groundwater?,” Plos One, Vol. 11, No. 10, p. e0164106, Oct. 2016, https://doi.org/10.1371/journal.pone.0164106
-
V. Frietze, R. Gioannini, M. Al-Ajlouni, D. Vanleeuwen, and R. Hilaire, “Contrasting urban landscapes and reduced irrigation engender water conservation in a desert environment,” Sustainability, Vol. 10, No. 3, p. 624, Feb. 2018, https://doi.org/10.3390/su10030624
-
M. Salvaggio, R. Futrell, C. D. Batson, and B. G. Brents, “Water scarcity in the desert metropolis: how environmental values, knowledge and concern affect Las Vegas residents’ support for water conservation policy,” Journal of Environmental Planning and Management, Vol. 57, No. 4, pp. 588–611, Apr. 2014, https://doi.org/10.1080/09640568.2012.756806
-
E. P. Kearsley and P. J. Wainwright, “Porosity and permeability of foamed concrete,” Cement and Concrete Research, Vol. 31, No. 5, pp. 805–812, May 2001, https://doi.org/10.1016/s0008-8846(01)00490-2
-
Z. Chen, Z. Z. Zhang, Z. H. Cong, L. N. Wang, and H. P. Wu, “Research and application progress of open-cell polymeric foams,” Journal of Materials Engineering, Vol. 48, No. 3, pp. 1–9, 2020.
-
E. K. K. Nambiar and K. Ramamurthy, “Influence of filler type on the properties of foam concrete,” Cement and Concrete Composites, Vol. 28, No. 5, pp. 475–480, May 2006, https://doi.org/10.1016/j.cemconcomp.2005.12.001
-
S. K. Jose, M. Soman, and Y. S. Evangeline, “Influence of mixture composition on the properties of foamed concrete,” Materials Today: Proceedings, Vol. 42, pp. 399–404, 2021, https://doi.org/10.1016/j.matpr.2020.09.592
-
W. Xu, X. Y. Liu, and Q. H. Zhu, “Experimental research on foam concrete panel prepared with chemical method used in external wall external insulation system,” Concrete, Vol. 3, pp. 131–134, 2012.
-
X. C. Luo and C. A. Wang, “Preparation and properties of slag-based gelpolymer porous materials,” Journal of the Chinese Ceramic Society, Vol. 44, No. 3, pp. 450–456, 2016, https://doi.org/10.14062/j.issn.0454-5648.2016.03.17
-
E. K. K. Nambiar and K. Ramamurthy, “Models relating mixture composition to the density and strength of foam concrete using response surface methodology,” Cement and Concrete Composites, Vol. 28, No. 9, pp. 752–760, Oct. 2006, https://doi.org/10.1016/j.cemconcomp.2006.06.001
-
N. Sebaibi, F. Khadraoui-Mehir, S. Kourtaa, and M. Boutouil, “Optimization of non-autoclaved aerated insulating foam using bio-based materials,” Construction and Building Materials, Vol. 262, p. 120822, Nov. 2020, https://doi.org/10.1016/j.conbuildmat.2020.120822
-
L. G. Xiao and J. Y. Mao, “Research on cement-based porous sound absorbing materials,” Northern Architecture, Vol. 4, No. 1, pp. 42–46, 2019.
-
M. Y. Hou, X. C. Zhu, G. Q. Li, Y. Zhang, and X. J. Lv, “Review on the research and application of foam concrete,” Bulletin of the Chinese Ceramic Society, Vol. 38, No. 2, pp. 410–416, 2019, https://doi.org/10.16552/j.cnki.issn1001-1625.2019.02.018
-
W. S. Zhao, W. Z. Chen, X. J. Tan, and S. Huang, “Study on foamed concrete used as seismic isolation material for tunnels in rock,” Materials Research Innovations, Vol. 17, No. 7, pp. 465–472, Nov. 2013, https://doi.org/10.1179/1433075x13y.0000000110
-
J. Lee and Y. C. Choi, “Pore structure characteristics of foam composite with active carbon,” Materials, Vol. 13, No. 18, p. 4038, Sep. 2020, https://doi.org/10.3390/ma13184038
-
T. Li, F. Huang, L. Li, J. Zhu, X. Jiang, and Y. Huang, “Preparation and properties of sulphoaluminate cement-based foamed concrete with high performance,” Construction and Building Materials, Vol. 263, p. 120945, Dec. 2020, https://doi.org/10.1016/j.conbuildmat.2020.120945
-
L. N. Wang, Z. Chen, and Z. Z. Zhang, “Influence of foaming agent on pore structure and water absorption property of slag-based geopolymer,” Bulletin of the Chinese Ceramic Society, Vol. 39, No. 7, pp. 2085–2091, 2020, https://doi.org/10.16552/j.cnki.issn1001-1625.2020.07.009
About this article
The authors gratefully acknowledge the financial support provided by Project funded by National Natural Science Foundation (Grant number 50772131), Key Project of Ministry of Education (Grant number 106086), Special Funding Project for Basic Research Business Fee of Central Universities (Grant number 2010YJ05).