Abstract
Analyzed the formation mechanism of longitudinal vibration of the submarine propulsion shafting system, and introduced its existing vibration control technology. The content included the improvement design of propulsion shafting system, new types of thrust bearing, composite material shaft, dynamic vibration absorber, phonon crystal band gap damping and relative active control technology. A new method for the application of metal rubber technology in thrust bearing was put forward, which provided a new idea for the research work in the future.
1. Introduction
To improve the stealth of the submarines, we need to reduce the vibration and noise of the submarine. The world had invested a lot of money to improve the performance of the submarine. At present, the submarine vibration and noise reduction device after several generations of technology development, had basically solved the vibration problem of the main power plant.
The vibration is transmitted to the outer shell through the thrust bearing, and the acoustic radiation caused by the acoustic radiation has a serious influence on the acoustic performance of the ship. The main channel of propulsion shaft longitudinal vibration transmission to the hull, including the support bearings, thrust bearing and its base. Feng Guoping [1] on the ship stern vertical excitation transfer characteristics were deeply analyzed, research showed that the thrust bearing base is the main transfer path to promote the longitudinal vibration of the shafting, so it can be taken control measures on the thrust bearing or its base to reduce the propeller drive force to the ship hull. However, due to the special installation position of the thrust bearing on the submarine and the special requirements for the reliable work of the propulsion shafting, the vibration reduction of the thrust bearing is a technical problem which has not been solved very well.
At present, the existing propeller shaft longitudinal vibration device was a huge volume, complex structure, poor reliability, and it was difficult to integrate with the thrust bearing and other significant shortcomings. Therefore, it is a key technology to reduce the vibration of the thrust bearing, which is the development of the submarine to low noise in our country. The development of high efficiency and high efficiency integrated longitudinal vibration reduction thrust bearing is an effective way to solve this problem.
Metal rubber was a kind of new material in recent years, scientists have invented, has high elasticity, high damping, high temperature, acid pollution, oil pollution, anti fatigue, aging and long life excellent physical and mechanical properties.
Therefore, as soon as possible to carry out efficient integration of embedded metal rubber damper longitudinal thrust bearing development has become an urgent and imminent research tasks, to reduce the noise level of submarine propulsion shafting longitudinal vibration caused, has important military significance to improve the performance of the submarine stealthy attack.
2. Body
2.1. Study on longitudinal vibration mechanism of propulsion shaft system
The ship propulsion shafting is the power delivered to the propeller, which causes the propeller to generate the thrust force and urges the ship to sail. When the ship sailing process, mix in the nonuniform of the flow field stern is inevitable, the propeller motion in the flow field mix causes pulsation excitation force, longitudinal force radial harmonic component plus the host device and propulsion shafting torsional vibration generated will cause the axial movement of the propulsion shafting reciprocating, this phenomenon is the axial vibration of ship shafting.
There are various excitation forces which affect the longitudinal vibration of the propulsion shafting system of the ship, in which the crankshaft of the engine produces the alternating longitudinal component after the bending and torsion deformation, and the longitudinal excitation of the propulsion shaft system is generated. The indirect excitation force are more occurred in the surface ship diesel engine shaft. The axial thrust of the propeller is the direct excitation force which causes the longitudinal vibration of the propulsion shaft system, and the weight of the propeller force in the longitudinal vibration of the propeller shaft is heavier. The propeller rotates in the uneven mixing flow field to produce the axial frequency pulsation exciting force of the harmonic frequency of the leaf frequency. In addition, the propeller manufacturing accuracy can also lead to propeller static imbalance, dynamic imbalance and hydrodynamic imbalance phenomena, also affect the thrust shaft longitudinal vibration.
Cfiertock [2] in the 1960s began to study propeller propulsion force transmission path, the results showed that more than 90 % of the propeller excitation force through the propulsion system is transmitted to the hull indirectly.
The research on the longitudinal vibration of submarine propulsion shafting system was focused on the characteristics of force transmission and the sound radiation of the hull caused by coupling vibration between propulsion system and hull structure. The United States began to study this problem in the 1950s, and had establish a complete analytical theory [3, 4].
In recent years, many domestic scholars have begun to pay attention to propeller shaft unsteady excitation caused by the longitudinal vibration of the shaft. The relevant universities and research institutes have carried out on the axial vibration of the longitudinal vibration mechanism analysis [5-8], research progress fast.
2.2. Study on passive control technology of longitudinal vibration of propulsion shaft system
For submarine propulsion shafting, the longitudinal vibration control research is focused on the secondary incentive force transferred to the hull through the thrust bearing.
GKN company proposed a new shaft design, the original strict alignment of the axis of the shaft line was designed to fold line type of shaft and in the corner with a special constant speed shaft, which was used to a certain extent, to make the shaft system become “soft” and to reduce the axial restraint of the shaft. The propeller pulsating force was attenuated effectively when it was transmitted along the shaft to the corner joint, which reduced the longitudinal vibration of the propulsion shaft system and the secondary excitation force transmitted to the hull [9].
The most economical and convenient way to control the longitudinal vibration of propulsion shafting is to change the material of the propulsion shaft system. The US Navy tried to use composite shafts instead of existing metal shafts in the 1990s [10]. Composites have a range of advantages over metal shafts: light weight, low cost, corrosion resistance, and electromagnetic interference resistance. The same type of composite shaft material than the metal shaft can save 25 %-80 % of the weight [11], which will undoubtedly have significant advantages to improve the speed of the ship.
By designing a new type of thrust bearing, the vibration transmission path can be changed and the longitudinal vibration of the propulsion shafting system and the secondary excitation force transmitted to the hull can be reduced at a certain extent. Shen Jianping [12] referred to bulkhead thrust bearings; Zhang Jinguo et al. [13] proposed a new type of flange-type thrust bearing. These thrust bearings were attached to the hull bulkhead directly so that the thrust force transmitted by the thrust bearing was transmitted evenly to the bulkhead. In addition, it is also possible to arrange the vibration-damping mass on the bulkhead to further improve the vibration control effect.
John [14] designed a new type of coaxial series thrust bearing, the coaxial series thrust bearings include internal and external bearings; there are two oil chambers, the inner bearing nested in the outer bearing oil chamber. The longitudinal vibration of the propulsion shaft was transmitted to the inner bearing through the thrust ring and then to the outer bearing through the inner bearing shell.
At present, many scholars used dynamic vibration absorber to reduce the longitudinal vibration of propulsion shaft system. The basic principle is to add a substructure (i.e., absorber) to the propulsion shafting system, by properly choosing the structural form, dynamic parameters and thrust shaft system to improve the vibration state of the propulsion shaft system, and then reduce the longitudinal vibration of the propulsion shaft system in the expected frequency band.
Goodwin [15] proposed using resonance converter (Resonance Changer) to reduce the longitudinal vibration of the propulsion shafting system, through dynamic tuned vibration will promote the natural frequency of longitudinal vibration of shafting for tuning frequency, reducing peak longitudinal vibration of propulsion shafting.
Dylejko [16-18] used Goodwin's theory of resonant converter to analyze the coupled system model including propeller, shaft system, resonant converter, thrust bearing and its base by using transfer matrix method. Since then, Merz [19, 20] on the basis of the Dyleiko research, continue to study the control effect of the resonant converter by the propulsion shaft longitudinal vibration caused by the hull underwater radiation.
In recent years, domestic scholars in reference to the results of foreign dynamic vibration absorber on the basis of the dynamic vibration absorber to carry out the relevant research work. Liu et al. [21] used Dyleiko's method of analyzing the longitudinal vibration transmission characteristics of propulsive shafting. The power flow was used to evaluate the energy transmitted to the hull by the longitudinal bearing of the thrust bearing, and the axial position damping effect. Li et al. [22] used the direct search algorithm of maximum minimization problem to optimize the parameters of the dynamic vibration absorber to reduce the longitudinal vibration of the propeller shaft system, and obtained the optimal value of the dynamic vibration absorber parameters so that the dynamic vibration absorber was within the design parameter range to make the best effect of the longitudinal vibration reduction.
Wang Jia-sheng [23] designed a centrifugal pendulum powered by a bracket, swing rod and other components of the mass absorber, directly installed in the shaft with the shaft rotates, its natural frequency can be changed by the mass of swing rod at both ends of the adjustment. Test results of the shafting test stand showed that the centrifugal pendulum dynamic vibration absorber can realize the longitudinal vibration reduction of the propulsion shaft system to a certain extent.
The local resonant band gap mechanism of phonemic crystals was first proposed by Liu et al. [24]. In determining the excitation frequency, local vibration and resonance of the original structure, the local vibration of elastic waves is generated with the original structure under the excitation of the vibration wave interaction in the outside, the incident wave can continue to spread in the structure, and then control the vibration in the structure transfer. As soon as the design of the low frequency band gap of the crystal is solved, the vibration reduction technology of the crystal band gap will be widely used in the field of vibration and noise reduction.
The installation of longitudinal shock absorber is an effective method to isolate longitudinal vibration. Yang Zhirong [25] designed an embedded marine thrust bearing longitudinal rubber shock absorber, the rubber damping block embedded in the thrust bearing shell dug out of the annular groove, in order to isolated the propeller pulsating thrust excitation caused by longitudinal vibration of shafting and then to the hull transmission force.
He Lin proposed a possible way to integrate the thrust bearing and the power device to solve the problem of thrust bearing vibration isolation by using the large scale low frequency vibration isolation device. This method can be used to transform the concentrated force of the thrust bearing into the dispersion force of the hull.
2.3. Study on active control technology of longitudinal vibration of propulsion shaft system
The end of 1990s, the United States took the lead in promoting the vertical vibration of the shafting system active control technology. Lewis studied the active control technology of propulsion shafting longitudinal vibration of the submarine, and proposed a design scheme of magnetic thrust bearing composed of magnetic thrust ring, magnet and its accessories. The magnetic force between the magnetic thrust ring and the magnet can partially counteract the propulsive pulsating force transmitted by the propeller shaft, thereby reducing the longitudinal vibration of the propulsion shafting.
Baz developed the pneumatic servo active control technology research of propulsion shaft longitudinal vibration. They first established the theoretical model to analyze the control effect of the pneumatic servo active control system on the longitudinal vibration of the propulsion shaft system under different excitation conditions. Then the prototype of the pneumatic servo actuator was developed and installed on the simulated shafting system. The test results showed that the active control effect in the low frequency range.
Johnson designed an electromagnetic active control device, the electromagnetic actuator includes magnetic heat treatment after cold rolling of the inner core and double winding coil, the inertial mass (composed of iron, a permanent magnet and an outer sleeve) and annular shrapnel and other components, the inner core is directly fixed on the shaft and rotates with the shaft. Through the arrangement of the acceleration sensor, force sensor and rotational speed on the shafts, shaft longitudinal vibration acceleration signal and force signal and speed were measured and the measuring signal through the filter amplifier transmitted to the controller, the controller according to a control algorithm (not specified in the literature) to calculate the control signal is transmitted to the electromagnetic actuator, electromagnetic the corresponding magnetic actuator and produced in the inertial mass and the inertial mass do micro vibration in its equilibrium position, produce control force in the opposite direction of the longitudinal vibration of coaxial lines, thereby reducing the longitudinal vibration of shafting. The active electromagnetic control device was essentially the excitation force by axial pulsation Lorenz force to offset propeller alternating, connected with the propulsion shaft in parallel, and the inertial mass as the actuator, the smaller the adverse effects of shafting.
At present, there were few researches on the active control technology of longitudinal vibration of propulsion shaft system. Zhan Yong designed a similar active control device by referring to Johnson’s basic idea. Zeng Gewei carried out semi-active control simulation analysis on the longitudinal vibration of propulsion shafting system. The simulation results showed that the installation of MR damper can effectively reduce the longitudinal vibration of propulsion shafting.
2.4. Embedded metal rubber thrust bearing
Metal-rubber is a kind of mechanical structural parts that are particularly suitable for the needs of aerospace technology. It was named for having a rubber elastic, but it was made of metal, not volatilize in the vacuum, not afraid of radiation environment, the ability of high temperature and low temperature, so instead of rubber to do vibration, damping and seals have great benefits on improving aerospace product life, reliability and performance.
Embedded metal rubber thrust bearing, as shown in Fig. 1. The longitudinal thrust shafting by thrust pad transfer to the thrust block, thrust block and shell ring clearance, annular groove metal rubber damping block is embedded in the bearing shell corresponding thrust block collar dug inside, damping block circle symmetrically with the same quantity and the thrust pad, so the longitudinal thrust is transferred to the metal the rubber damping block by block thrust ring, and then passed to the thrust bearing shell through the metal rubber damping block, the longitudinal vibration of marine shafting is isolated.
Fig. 1Embedded metal rubber thrust bearing principle diagram
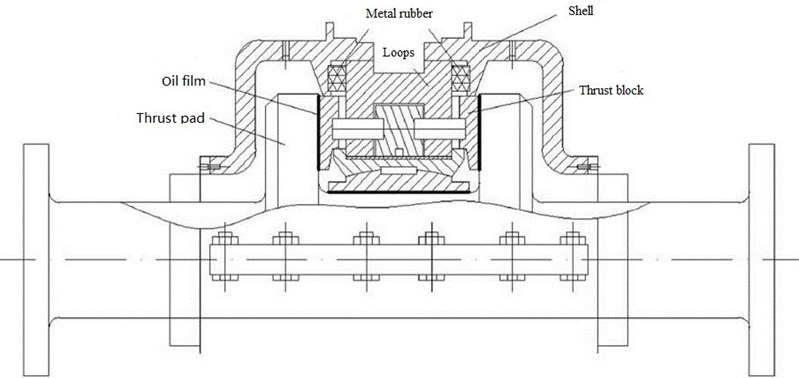
At present, the metal rubber products in the space large-scale robot arm and antenna, satellite laser angle reflector, sounding rocket Langmuir probe, aero-engine pipeline, combat aircraft electronic equipment and fire control system, unmanned reconnaissance machine photoelectric platform, Large-scale surface warships optoelectronic devices, submarine optoelectronic masts and auxiliary equipment and pipelines, torpedo launching and power devices, large transformers, earthquake and typhoon-prone areas of power transmission tower, the installation of precision equipment construction has been batch applications.
3. Conclusions
Improve the stealth performance of the Navy submarine is imminent. Submarine vibration and noise reduction is the key to improve its stealth performance, submarine vibration and noise reduction device has experienced several generations of technology development, the problem of the main power plant has been basic solved.
The study of longitudinal vibration and its control technology of submarine propulsion shafting was the focus of naval research at home and abroad, and the published papers are few because of military secrets. Therefore, effective technical means must be taken to control the vibration of the thrust bearing, to promote the development of quiet and low noise of submarines in China. With the maturity of metal rubber theory, the application of metal rubber to the new thrust bearing is a research direction, which can solve the noise problem caused by longitudinal vibration of propulsion shaft system on submarine.
References
-
Feng G., Zhan Y., Huang X., et al. Study on transmission path sin submarine stern excited longitudinal. Noise and Vibration Control, Vol. 6, 2009, p. 132-135.
-
Cfiertock G. Forces on a submarine hull induced by the propeller. Journal of Ship Research, Vol. 9, Issue 2, 1965, p. 122-130.
-
Riigby C. P. Longitudinal vibrations of marine propeller shafting. Transactions of the Institute of Marine Engineers, Vol. 60, 1948, p. 67-78.
-
Kane J. R., McGoldrick R. T. Longitudinal vibrations of marine propulsion-shafting systems. Transactions of the Society of Naval Architects and Marine Engineers, Vol. 57, 1949, p. 193-252.
-
Cao Y. P. Study on Underwater Structure Vibration and Radiated Noise Control Caused by Propeller Exciting Force. Harbin Engineering University, Harbin, 2008.
-
Li L. W., Zhao Y., Zhang G. B. Research of axial coupling vibration characteristic of marine shaft test bed. China Steel Structures Society of Ocean Steel Branch, Conference and Proceedings of the Sixth Council Third Session, Luoyang, 2010.
-
Wang J. S., Liu Y. Z. Test and analysis of axial vibration hypostatic test rig of the ship’s propelling shafting. Electrical Mechanical Engineering Branch of China Electronic Society, Mechatronics Academic Conference Proceedings, 2009.
-
Xie J. R., Wu Y. S., Shen S. G. Transmission character of propeller excitation through shaft-line system to hull. China Shipbuilding, Vol. 52, Issue 1, 2011, p. 80-89.
-
Lago T., Winberg M., Johansson S. Active vibration isolation in ships: source identification and ANVC approach. 5th International Congress Sound and Vibration, Adelaide, Australia, 1997.
-
Wilhelmi G. F., Appleman W. M., Loof T. C. Composite shafting for naval propulsion systems. Naval Engineers, Vol. 98, Issue 4, 1986, p. 129-136.
-
Mouritz A. P., Gellert E., Burchill P., et al. Review of advanced composite structures for naval ships and submarines. Composite Structures, Vol. 53, 2001, p. 21-41.
-
Shen J. P., Zhou W. J., Tong Z. P. Status and trends about research of vibration control in ship transmitting device. Ship Science and Technology, Vol. 32, Issue 8, 2010, p. 7-12.
-
Zhang J. G., Yao S. W., Wang J. Research on vibration transfer characteristics of flanged thrust bearing. Noises and Vibration Control, Vol. 2, 2008, p. 23-26.
-
John E., Schaefer W. Thrust Bearing System for Counter-Rotating Propeller Shafts, Particularly Ships Propeller Shafts. U.S. Patent No. 4993848, 1991.
-
Goodwin A. J. H. The design of a resonance changer to overcome excessive axial vibration of propeller shafting. Institute of Marine Engineers Transactions, Vol. 72, 1960, p. 37-63.
-
Dylejko P. G., Kessissoglou N. Minimization of the vibration transmission through the propeller-shafting system in a submarine. Journal of the Acoustical Society of America, Vol. 116, Issue 4, 2004, p. 25-69.
-
Dylejko P. G., Kessissoglou N., Tso Y., et al. Optimization of a resonance changer to minimize the vibration transmission in marine vessels. Journal of Sound and Vibration, Vol. 300, 2007, p. 101-116.
-
Dylejko P. G. Optimum Resonance Changer for Submerged Vessel Signature Reduction. University of New South Wales, Sydney, 2007.
-
Merz S., Kessissoglou N., Kinns R., et al. Optimization of a submarine's resonance changer using the method of moving asymptotes. Proceedings of Acoustics, Adelaide, Australia, 2009.
-
Merz S., Kessissoglou N., Kinns R., et al. Minimization of the sound power radiated by a submarine through optimization of its resonance changer. Journal of Sound and Vibration, Vol. 329, 2010, p. 980-993.
-
Liu Y. Z., Wang N., Meng H., et al. Optimization of dynamic absorber parameters for reducing axial vibration of ship shafting. Journal of Vibration and Shock, Vol. 28, Issue 5, 2009, p. 184-189.
-
Li L. W., Zhao Y., Lu P., et al. Power damper parameters optimization for reducing longitudinal vibration of ship shafting. Ship Building of China, Vol. 51, Issue 2, 2010, p. 139-148.
-
Wang J. S. Experimental research on longitudinal vibration reduction technology of submarine propulsion shaft system based on principle model. National University of Defense Technology, Changsha, 2009.
-
Liu Z. Y., Zhang X. X., Mao Y. W., et al. Locally resonant sonic materials. Science, Vol. 289, 2000, p. 1734-1736.
-
Yang Z. R., Qin C. Y., Rao Z. S., et al. Design of vibration isolator in ship’s thrust bearing. Noise and Vibration Control, Vol. 33, Issue 6, 2013, p. 211-215.